Measuring Noise Levels: A Critical Factor in Worksite Safety
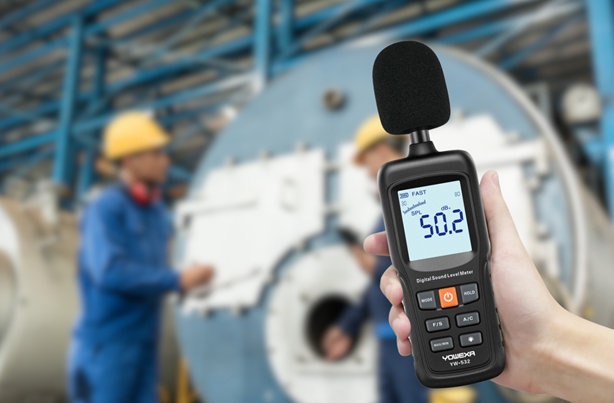
Noise level measurement in the workplace is one of the important practices in industries that involve high levels of exposure to noise on a daily basis. The high level of noise can seriously affect health by causing irreparable damage to hearing, reducing concentration, increasing stress, and even being a contributor to workplace accidents. NIHL is one of the top causes of preventable occupational diseases. Effective hazard control requires employers to be proactive through regular measurement of noise levels and application of appropriate controls. It identifies why noise level measurement is necessary; tools and techniques used; and best practices for workplace safety and compliance with relevant regulations.
Noise in the workplace can be more than just a nuisance; it is a direct threat to employee health and safety. Long-term exposure to high noise levels can cause permanent damage, even at levels considered moderately loud. According to Safe Work Australia, exposure to more than 85 decibels (dB) for more than an 8-hour workday may cause damage to a person’s hearing. Even sudden peak noise levels above 140 dB can cause immediate hearing loss.
Besides all the hearing-related problems, too much noise can lead to low productivity of employees, poor communication, and a reduction in concentration. Many employees working in a high level of noise find it very difficult to listen properly to instructions, warnings, or alarms, hence leading to potential accidents. Accurate measurement of the noise level permits the employer to spot troublesome areas and take necessary noise control measures to safeguard the health and welfare of employees.
Legal Requirements for Noise Measurement in Australia:
In Australia, the Work Health and Safety (WHS) Regulations 2011 outline the legal requirements that must be undertaken to manage noise within the workplace. It requires employers to conduct noise assessments with the aim of ensuring that the workers’ exposure to noise does not exceed the national exposure standard. Limits set by regulations include:
- 85 decibels (dB) over an 8-hour shift – referring to average exposure.
- 140 decibels (dB) for a single peak noise event.
Where the noise levels exceed these upper limits, employers are forced to act immediately so as to reduce noise exposure and meet the relevant legal standards. Noise measurement on a routine basis is one of the key tools that could effectively be employed to fulfill the twin goals of compliance and prevention of noise-related health problems within the workforce.
Noise Measurement Procedure:
Noise level measurement involves a systematic evaluation of the intensity of sound in various areas of the workplace. It is done with the assistance of specialized equipment, which picks up and measures the levels of noise exposure. The successive process for noise exposure mapping is highlighted below:
1. Identification of Areas Exposed to Potential High Levels of Noise
First, the areas in the workplace that could lead to noise exposure need to be identified. These are normally settings where loud machinery or equipment could be used, such as construction sites, manufacturing floors, mining operations, and workshops. Common sources of noise include power tools, engines, compressors, and heavy machinery.
For identification of high-risk areas, employers should take into consideration both the steady-state noise-that is, constant noise from equipment-and also intermittent noise, which may be from alarms, vehicle horns, or even explosions.
2. Select the Right Measurement Equipment
Once the potential noise hazards have been identified, appropriate measurement tools should be selected. The most common instruments used in measuring noise include:
Sound Level Meters (SLMs): SLMs measure noise at a specific location at a given point in time. The best uses for SLMs include measuring environmental noise and identifying “hot spots” where the noise level is highest.
Noise Dosimeters: Noise dosimeters are small devices that workers can wear while working in the field. Dosimeters measure individual noise exposure over time. It gives a very accurate picture of daily exposure for workers in an area where noise levels are constantly changing.
3. Conduct Noise Measurement
The noise measurements should be done at several locations in the workplace, especially in those locations where workers usually stay for more extended periods or noisy equipment is erected. Noise measurement should consider both average exposure over a representative period-8 hours, and also peak noise levels for sudden loud events.
For validity of measurement results, it is desirable that the measurements are made when machinery is under normal operating conditions, operating as it would during a normal workshift. Noise measurements shall include all sources of noise, both continuous and intermittent.
4. Analyze the Results
The measured noise has to be analyzed and compared with the Work Health and Safety exposure limits once the noise measurements have been made. Where the workplace exceeds the legal standard for exposure of 85 dB over 8 hours, or at 140 dB for peak events, action is required to reduce the noise level.
Noise consultants or occupational hygienists can assist such an analysis, with the aid of advanced acoustic modeling techniques to assess the overall noise profile of the workplace and advise on suitable noise control strategies.
5. Noise Control Measures
The result of a noise assessment might reveal that workers are exposed to hazardous levels of noise; under these circumstances, employers are under legal obligation to reduce exposure. Noise control measures include:
- Engineering Controls: Modify or replace noisy equipment with quieter ones, install noise barriers, and add soundproofing materials. Administrative Controls: Rotate workers in high-noise and low-noise areas, reduce time in noisy areas, and schedule the noisiest tasks when the fewest number of workers are present. Personal Protective Equipment (PPE): Provide earplugs or earmuffs for workers when noise cannot be adequately reduced through engineering controls or administrative controls.
6. Monitor and Review Noise Levels Regularly
Noise levels should be regularly monitored, particularly when changes have been made to work processes or there has been the introduction of new equipment. Regular noise assessments ensure the control measures remain effective and the workers are adequately protected against harmful noise exposure.
Best Practices for Noise Level Measurement:
In order for the proper measurement of noise level to be observed and WHS regulations adhered to, there are some best practices that businesses must undertake to include:
1. Hire Qualified Professionals
The company needs to hire a noise consultant or occupational hygienist who holds nationally recognized certification to ensure the validity of noise measurement and is taken under legal conformance. By hiring a qualified professional, one can assure that the competencies and equipment for proper assessments are there, together with recommendations about noise controls.
2. Conduct Regular Assessments
Noise levels at work vary with time due to the wear and tear of equipment, new machinery, or changes in work procedures. Regular assessments spot new risks and help in maintaining protection for workers.
3. Involve Workers in the Process
Workers are often the best early detectors of any noise problems. Worker involvement in the noise assessment process can also be useful in highlighting those specific areas where noise is considered to be a problem. Workers should also receive training on how to identify hazardous noise levels and how to properly use their hearing protection.
4. Maintain Detailed Records
Employers should retain records of all noise assessments, the locations measured, equipment used, and the results. This helps in monitoring progress in exposure to noise over time and as proof that WHS requirements have been complied with.
Conclusion:
Noise measurement at the workplace is an important process in terms of protection against the hazardous effects of excessive noise exposure. Standard periodic noise assessments help employers to identify potentially hazardous areas, realize ways in which effective control measures should be implemented, and fulfill the legal standards required regarding noise. Giving due priority to noise management allows business organizations to have a safer, healthier, and productive work environment.
Stay Connected with: trustblogs